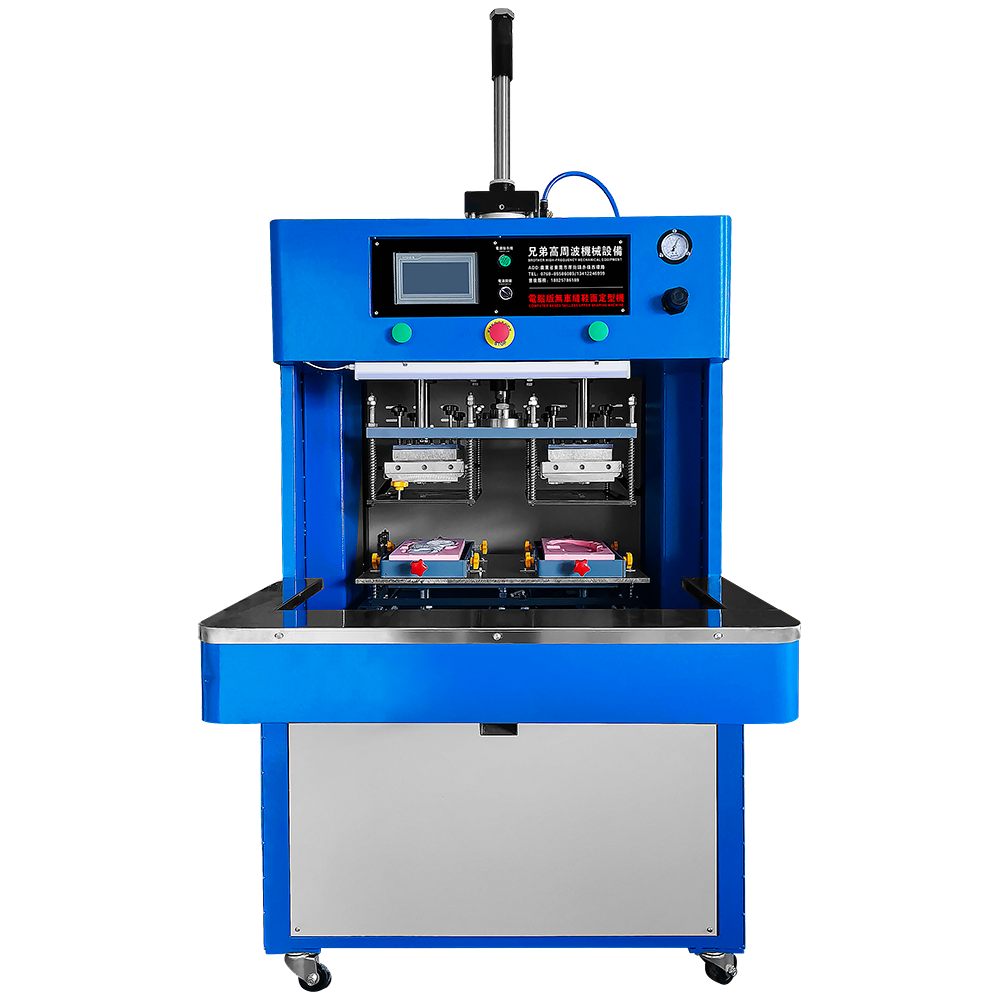
Single station hot cutting machine
Intelligent temperature control, precise fitting! Single-station hot-cutting outsole machine (computer version)
The single-station hot-cutting outsole machine (computer version) is specially designed for seamless upper lamination and 4D upper craftsmanship. It achieves high-precision hot cutting and bonding through intelligent temperature control and automated operation. Equipped with a PLC human-machine interaction system, one-button start, full temperature monitoring, no glue overflow and no deformation of the finished product, helping shoemaking companies to upgrade efficiently!
Core parameters and performance highlights:
Power configuration: 480W power, 380V three-phase five-wire power supply, stable adaptation to industrial scenarios.
Heating system:
Heating plate: 180×400mm large area uniform heating, quickly heating to the set temperature.
Temperature control accuracy: 12-way temperature detection + 2-way dual-station mold temperature measurement, temperature error ≤±1℃.
Operation design:
Working height: 840mm ergonomic, reducing operator fatigue.
Stroke range: 150mm flexible adjustment, suitable for processing of shoe materials of different thicknesses.
Safety protection: automatic alarm for abnormal temperature, no mold opening if not up to standard, eliminating the risk of defective products.
Appearance size: 1350×930×2150mm compact body, saving workshop space.
Core functions and advantages:
✅ Intelligent temperature control: digital temperature detection system, real-time display of heating effect, precise control of hot cutting quality.
✅ One-button operation: automatic in and out mold design, simplified process, and increased production efficiency by 40%.
✅ Widely compatible: Suitable for EVA, TPU, rubber outsole and other materials, supporting 4D upper lamination, sports shoe upper bonding and other processes.
✅ Durable and energy-saving: Industrial-grade cylinders (100×150mm) are resistant to high pressure, with a continuous operating life of more than 80,000 hours and energy consumption reduced by 25%.
Applicable scenarios and industries:
Shoemaking industry: hot cutting of sports shoe outsoles, three-dimensional lamination of 4D uppers, and seamless bonding of waterproof shoes.
Shoe material processing: insole molding, precise hot pressing of sole decorative parts.
Customized shoes: hot cutting and bonding of personalized patterns on high-end uppers.
Simplified operation process:
Parameter setting: set temperature, pressure, and time through the human-machine interface, and 12-way temperature control templates are calibrated synchronously.
Material positioning: place the upper and outsole on a 180×400mm heating plate and clamp them automatically.
One-button start: PLC controls automatic entry and exit of the mold, 150mm stroke high-pressure hot cutting, and no manual intervention is required throughout the process.
Finished product inspection: Automatic mold opening when the temperature reaches the standard, neat edges without burrs, and directly enter the quality inspection stage.
Product core advantages:
High-precision guarantee: dual-station mold temperature measurement system, accurate fitting position, finished product qualification rate ≥ 99%.
Safe and efficient: Instant alarm for abnormal temperature, anti-scalding design, zero operating risk.
Flexible adaptation: Supports rapid mold replacement, switching production tasks within 5 minutes, and responding to diversified order requirements.
Consult now to obtain exclusive solutions for single-station hot-cut outsole machine (computer version) and open a new chapter of efficient and seamless fitting!